- اف ای پاورتولز | FE Powertools
- ایبناشتاک | Eibenstock
- جپسون | Jepson
- بی دی اس | BDS
- بوش | Bosch
- متابو | Metabo
- پروموتک | Promotech
- یوروبور | Euroboor
- رپتور | Rotabroach
- فاین | Fein
- ایجیپی | AGP
- میلواکی | Milwaukee
- آ ا گ | AEG
- نیتو | Nitto
- دزنت | Dezent
- ایاستی پاور | AST Power
- تیری کیگو | 3Keego
- بی ام الکتریک | BM Electric
- محک | Mahak
مقایسه دریل مگنت و دریل ستونی؛ انتخاب صحیح برای پروژههای صنعتی
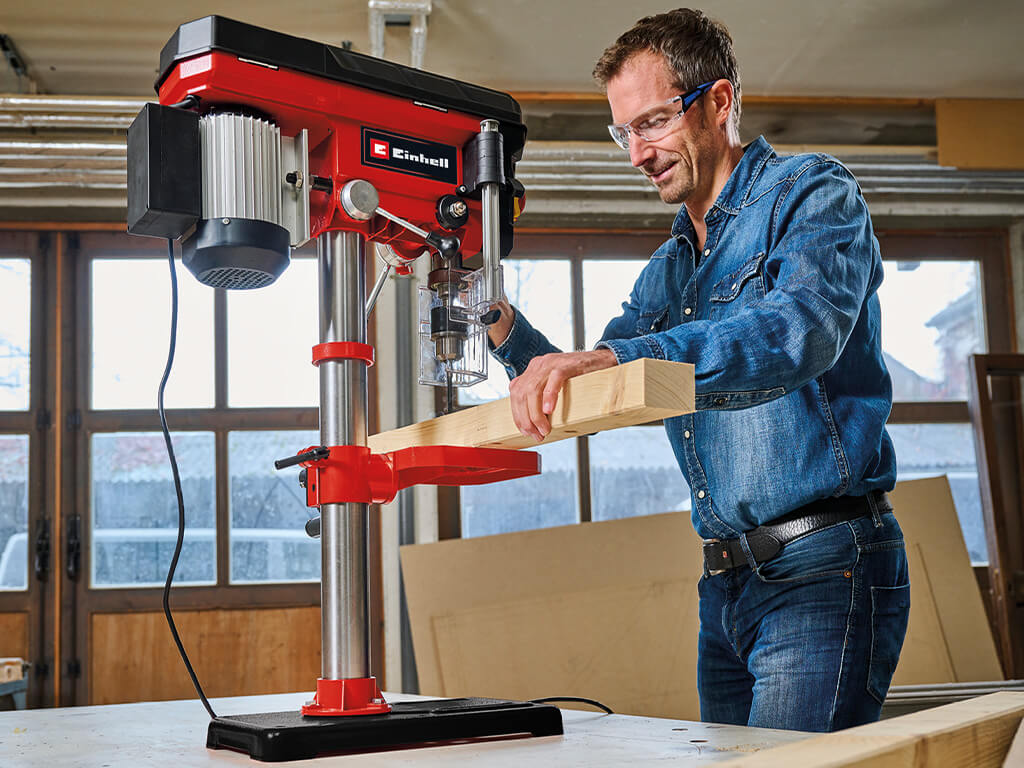
مقایسه دریل مگنت و دریل ستونی؛ انتخاب صحیح برای پروژههای صنعتی
مقدمه
دریل مگنت و دریل ستونی هر دو از ابزارهای کلیدی در صنایع فلزی و کارگاههای صنعتی محسوب میشوند. هرچند هدف اصلی هر دو دستگاه سوراخکاری دقیق فلزات است، اما تفاوتهای اساسی در ساختار، قابلیتها و کاربردهای آنها وجود دارد. انتخاب صحیح بین این دو گزینه میتواند به افزایش بهرهوری، کاهش هزینهها و بهبود کیفیت پروژههای صنعتی کمک کند.
در این مقاله، به صورت تخصصی به مقایسهی دریل مگنت و دریل ستونی میپردازیم. بررسی ویژگیهای فنی، کاربردهای رایج، مزایا و معایب هر دستگاه، و تحلیل هزینهها از جمله مباحثی است که در ادامه به آنها پرداخته خواهد شد. اگر در انتخاب ابزار مناسب برای پروژههای خود دچار تردید هستید، مطالعهی این راهنما میتواند دید کاملی به شما ارائه دهد.
معرفی کوتاه دریل مگنت و دریل ستونی
دریل مگنت و دریل ستونی از پرکاربردترین ابزارهای سوراخکاری صنعتی به شمار میآیند. هر کدام از این دستگاهها با هدف پاسخگویی به نیازهای متفاوت در محیطهای صنعتی طراحی شدهاند و ویژگیهای خاص خود را دارند.
دریل مگنت، دستگاهی قابل حمل است که به کمک پایهی مغناطیسی خود روی سطوح فلزی ثابت میشود. این ویژگی به کاربر امکان میدهد بدون نیاز به میز کار ثابت یا فیکسچر، عملیات سوراخکاری دقیق را حتی روی قطعات بزرگ یا در موقعیتهای دشوار انجام دهد. وزن سبکتر، قابلیت حمل آسان، و انعطافپذیری در کار از مزایای اصلی دریل مگنت محسوب میشوند. این دستگاهها معمولاً در پروژههای ساختوساز فلزی، مونتاژ سازهها، پلسازی و تعمیرات صنعتی به کار میروند.
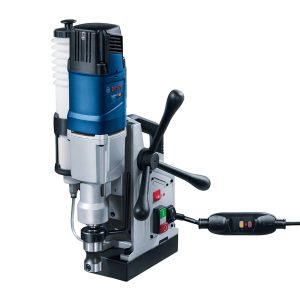
دریل مگنت چیست؟
در مقابل، دریل ستونی یک دستگاه ثابت و سنگینتر است که به صورت عمودی روی میز یا کف کارگاه نصب میشود. این دستگاه برای سوراخکاری دقیق و مداوم در کارگاههای تولیدی و صنعتی استفاده میشود. دریل ستونی از نظر دقت، ظرفیت و قدرت سوراخکاری نسبت به بسیاری از دستگاههای قابل حمل برتری دارد، اما به دلیل ابعاد بزرگتر و نیاز به فضای ثابت، کاربرد آن در پروژههای خارج از کارگاه محدود است.
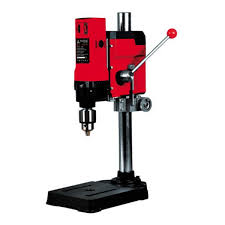
دریل ستونی چیست؟
درک تفاوتهای بنیادی بین دریل مگنت و دریل ستونی، پایهی تصمیمگیری صحیح برای انتخاب ابزار مناسب در پروژههای صنعتی است. در ادامهی این مقاله، به صورت تخصصی به مقایسهی این دو دستگاه در ابعاد مختلف خواهیم پرداخت.
مقایسه فنی بین دریل مگنت و دریل ستونی
دریل مگنت و دریل ستونی از نظر ویژگیهای فنی تفاوتهای قابل توجهی دارند که بر نحوهی کاربرد آنها در پروژههای صنعتی تاثیرگذار است.
از نظر قدرت، دریلهای ستونی معمولاً موتورهای قویتری دارند و قادرند سوراخهای بزرگتر و عمیقتر روی انواع فلزات سخت ایجاد کنند. این دستگاهها به دلیل ثبات و وزن بالاتر، برای انجام سوراخکاریهای پیوسته و طولانی مدت در محیطهای کارگاهی ایدهآل هستند. در مقابل، دریلهای مگنتی به لطف طراحی قابل حمل و پایه مغناطیسی خود، امکان سوراخکاری در موقعیتهای مختلف و روی سطوح بزرگ فلزی را فراهم میکنند. هرچند قدرت موتور در دریل مگنت نسبت به دریل ستونی محدودتر است، اما برای بسیاری از کاربردهای صنعتی روزمره کاملاً کافی به نظر میرسد.
از لحاظ ظرفیت سوراخکاری، دریلهای ستونی معمولاً در ابعاد و قطرهای بزرگتر تخصص دارند. این دستگاهها میتوانند سوراخهایی با دقت بالا و قطر زیاد در صفحات ضخیم فلزی ایجاد کنند. دریلهای مگنتی بیشتر برای سوراخکاری در ابعاد متوسط طراحی شدهاند و برای کار در محیطهای محدود و دشوار مناسبتر هستند.
دقت سوراخکاری در دریل ستونی به دلیل ثبات ساختاری بیشتر و وجود سیستم هدایت عمودی قویتر، بالاتر است. این دستگاهها برای پروژههایی که نیاز به انحراف حداقلی در فرآیند سوراخکاری دارند، انتخاب مناسبی به شمار میآیند. با این حال، دریلهای مگنتی مدرن با فناوریهای بهبود یافتهای که در تثبیت مغناطیسی و هدایت مته دارند، توانستهاند فاصله دقت خود را با دریلهای ستونی تا حد زیادی کاهش دهند.
از نظر سرعت، دریلهای مگنت و دریلهای ستونی هر دو مجهز به قابلیت تنظیم سرعت متناسب با نوع متریال هستند. با این حال، تنظیمات پیشرفتهتر سرعت و گشتاور در دریلهای ستونی امکان کار روی طیف وسیعتری از مواد را فراهم میکند.
در مجموع، مقایسه فنی نشان میدهد که انتخاب بین دریل مگنت و دریل ستونی باید بر اساس نیاز پروژه، نوع متریال، حجم کار و شرایط محیطی انجام شود.
مقایسه کاربرد در پروژههای صنعتی
دریل مگنت و دریل ستونی، هر کدام بسته به نوع پروژه و شرایط کاری، کاربردهای متفاوتی دارند که آگاهی از آنها میتواند به انتخاب صحیح ابزار کمک کند.
دریل ستونی به دلیل ثبات بالا و ظرفیت بیشتر در سوراخکاری قطعات بزرگ و ضخیم، در کارگاههای ثابت صنعتی بسیار محبوب است. این دستگاهها برای تولیدات انبوه، خطوط مونتاژ، و پروژههایی که نیاز به سوراخکاریهای پیدرپی و دقیق دارند، گزینهی ایدهآلی به شمار میآیند. در کارگاههایی که حجم تولید بالا و نیاز به دقت بسیار زیاد وجود دارد، دریل ستونی به عنوان ابزار اصلی سوراخکاری مورد استفاده قرار میگیرد.
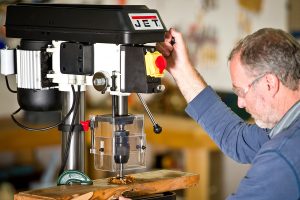
کاربرد دریل ستونی در پروژههای صنعتی
در مقابل، دریل مگنت برای پروژههایی که انعطافپذیری و قابلیت حمل اهمیت دارد، انتخاب بهتری است. این دستگاه در پروژههای ساخت و نصب سازههای فلزی، پلسازی، اسکلهسازی و تعمیرات صنعتی به کار میرود. قابلیت اتصال به سطوح عمودی یا حتی سقفی، دریل مگنت را برای سوراخکاری در موقعیتهای غیرمعمول و فضاهای محدود بسیار مناسب کرده است. به عنوان مثال، در پروژههای احداث پلهای فلزی یا نصب سازههای مرتفع، دریل مگنت به دلیل وزن کمتر و امکان کار در ارتفاع، کاربرد گستردهای دارد.
در پروژههای تعمیر و نگهداری صنعتی نیز، که نیاز به جابهجایی سریع تجهیزات و کار روی قطعات بزرگ در محل وجود دارد، دریل مگنت به دلیل طراحی قابل حمل خود مزیت قابل توجهی نسبت به دریل ستونی دارد. استفاده از دریل مگنت در محیطهای دور از کارگاه یا در محل پروژه، بهرهوری عملیات را به طور محسوسی افزایش میدهد.
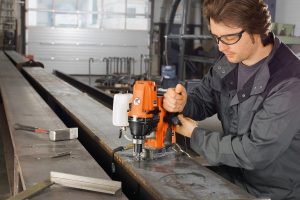
مقایسه کاربرد دریل مگنت در پروژههای صنعتی
در مجموع، دریل مگنت و دریل ستونی هر دو جایگاه خاص خود را در پروژههای صنعتی دارند. انتخاب بین آنها باید با توجه به ماهیت پروژه، میزان نیاز به دقت، حجم کار و شرایط محیطی صورت گیرد.
مقایسه هزینههای خرید و نگهداری دریل مگنت و دریل ستونی
هنگام انتخاب بین دریل مگنت و دریل ستونی، هزینههای خرید اولیه و هزینههای نگهداری بلندمدت از عواملی هستند که باید به دقت بررسی شوند.
از نظر قیمت خرید، دریلهای ستونی در ردههای مختلفی از نظر قدرت، ابعاد و کیفیت ساخت عرضه میشوند. مدلهای سادهتر ممکن است قیمت مناسبی داشته باشند، اما نمونههای حرفهای و سنگینتر میتوانند هزینهی قابل توجهی به همراه داشته باشند. دریل ستونیهای صنعتی که برای سوراخکاری قطعات بزرگ فلزی طراحی شدهاند، معمولاً نیاز به سرمایهگذاری اولیه بالاتری دارند.
دریلهای مگنتی به دلیل طراحی قابل حمل و فناوریهای خاص در ساخت پایه مغناطیسی، در برخی مدلها قیمتی نزدیک به دریلهای ستونی دارند. با این حال، به طور کلی در پروژههایی که نیاز به جابهجایی و انعطافپذیری بیشتری وجود دارد، ارزش افزودهی قابل توجهی ایجاد میکنند که هزینهی بالاتر را توجیه میکند.
از نظر هزینههای نگهداری، دریلهای ستونی به دلیل ساختار سادهتر و ثبات بیشتر، معمولاً نیاز به تعمیرات و سرویسهای کمتری دارند. در مقابل، دریلهای مگنتی به دلیل درگیری بیشتر قطعات مکانیکی، پایه مغناطیسی و مدارهای الکتریکی خاص، نیازمند سرویسهای دورهای دقیقتری هستند. نگهداری صحیح از پایه مغناطیسی و کنترل منظم سلامت موتور و کلیدهای برق در دریل مگنت اهمیت ویژهای دارد.
همچنین، هزینهی قطعات یدکی در دریل مگنت ممکن است کمی بالاتر از دریلهای ستونی باشد، به خصوص اگر از برندهای معتبر و تجهیزات اورجینال استفاده شود. با این حال، این هزینهها در برابر مزایایی که در پروژههای متحرک و خارج از کارگاه ایجاد میشود، منطقی به نظر میرسد.
در مجموع، تحلیل هزینههای خرید و نگهداری نشان میدهد که انتخاب بین دریل مگنت و دریل ستونی باید نه تنها بر اساس قیمت اولیه، بلکه با در نظر گرفتن هزینههای بلندمدت، میزان استفاده، نوع پروژه و شرایط محیطی صورت گیرد.
مزایا و معایب دریل مگنت و دریل ستونی
شناخت دقیق مزایا و معایب دریل مگنت و دریل ستونی به کاربران کمک میکند تا بر اساس نیازهای پروژه و شرایط کاری، انتخاب بهینهای داشته باشند.
یکی از بزرگترین مزایای دریل مگنت، قابلیت حمل و استفاده در موقعیتهای مختلف است. این دستگاهها به دلیل پایهی مغناطیسی قدرتمند، امکان سوراخکاری روی سطوح افقی، عمودی و حتی سقفی را فراهم میکنند. وزن نسبتاً کم، انعطافپذیری در جابهجایی، و سرعت نصب بالا، دریل مگنت را به گزینهای ایدهآل برای پروژههای ساخت و نصب در محل تبدیل کرده است. از سوی دیگر، قدرت مغناطیسی پایه ممکن است در برخی شرایط خاص، مانند سطوح زنگزده یا ضخامتهای کم فلز، کاهش یابد که این مساله یکی از محدودیتهای مهم دریل مگنت به شمار میرود.
در مقابل، دریل ستونی به دلیل ساختار ثابت و پایدار، دقت سوراخکاری بسیار بالاتری ارائه میدهد. این دستگاهها برای پروژههایی که نیاز به سوراخهای همراستا، دقیق و یکنواخت دارند، انتخاب بهتری هستند. دریل ستونی به دلیل ابعاد بزرگتر و وزن زیاد، قابلیت حمل ندارد و به محیطهای کارگاهی محدود میشود. این موضوع استفاده از آن را در پروژههای سیار یا در محل نصب سازهها دشوار میکند.
از نظر نگهداری، دریلهای مگنتی به دلیل وجود سیستمهای الکتریکی و مغناطیسی پیشرفته، نیازمند مراقبتهای دقیقتری هستند. هرگونه نقص در مدارهای الکتریکی یا آسیب به پایه مغناطیسی میتواند کارایی دستگاه را تحت تاثیر قرار دهد. در مقابل، دریلهای ستونی به دلیل طراحی سادهتر، استهلاک کمتری دارند و معمولاً با هزینههای کمتری نگهداری میشوند.
در نهایت، انتخاب بین دریل مگنت و دریل ستونی بستگی به اولویتهای پروژه، میزان نیاز به دقت، قابلیت حمل، و نوع محیط کاری دارد. هر یک از این دستگاهها، در صورت استفاده صحیح و متناسب با ویژگیهای فنی خود، میتوانند بازدهی مطلوبی در پروژههای صنعتی ایجاد کنند.
چه زمانی دریل مگنت انتخاب بهتری است؟
با توجه به مقایسههای فنی و کاربردی انجام شده، دریل مگنت و دریل ستونی هرکدام نقاط قوت خاص خود را دارند. اما در برخی شرایط، استفاده از دریل مگنت انتخاب منطقیتر و کارآمدتری خواهد بود.
در پروژههایی که نیاز به جابهجایی سریع تجهیزات، سوراخکاری روی سازههای بزرگ یا کار در موقعیتهای خاص مانند سطوح عمودی یا سقف وجود دارد، دریل مگنت بهترین گزینه محسوب میشود. وزن سبکتر، قابلیت حمل آسان و امکان اتصال مستقیم به قطعات فلزی بزرگ باعث میشود که دریل مگنت در محیطهای متغیر و خارج از کارگاه کارایی بیشتری داشته باشد.
همچنین در پروژههای ساخت و نصب سازههای فلزی مانند پلها، اسکلهها، خطوط لوله و سازههای صنعتی سنگین، استفاده از دریل مگنت به دلیل انعطافپذیری بالاتر، سرعت اجرا را افزایش میدهد و نیاز به فیکسچرهای پیچیده را حذف میکند. در محیطهایی که فضای کار محدود است یا نیاز به انجام عملیات سوراخکاری در ارتفاع وجود دارد، حمل یک دستگاه دریل ستونی عملاً غیرممکن خواهد بود و دریل مگنت به راحتی این خلأ را پر میکند.
در تعمیرات صنعتی نیز که دسترسی به قطعات و سطوح مختلف اهمیت بالایی دارد، دریل مگنت انتخاب مناسبی است. این دستگاه امکان سوراخکاری دقیق و سریع روی قطعات موجود را بدون نیاز به انتقال آنها به کارگاه فراهم میکند، که به صرفهجویی در زمان و هزینه کمک شایانی میکند.
با این حال، در پروژههایی که حجم بالایی از سوراخکاریهای مکرر با دقت بسیار بالا مورد نیاز است و فضای ثابت کارگاهی وجود دارد، دریل ستونی همچنان انتخاب بهتری خواهد بود. بنابراین تصمیم نهایی باید بر اساس ارزیابی دقیق نیازهای پروژه، محدودیتهای محیطی و اولویتهای فنی صورت گیرد.
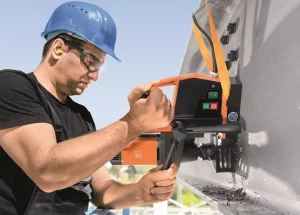
چه زمانی دریل مگنت انتخاب بهتری است؟
نمونههایی از پروژههای واقعی با دریل مگنت و دریل ستونی
در پروژههای ساخت پلهای فلزی بزرگ، مانند پل کابلی تبریز، استفاده از دریلهای مگنتی برای سوراخکاری تیرها و اتصالات فلزی به طور گسترده رایج است. در این نوع پروژهها، به دلیل نیاز به کار در ارتفاع، محدودیت فضای کاری و حجم زیاد اتصالات فلزی، حمل و استفاده از دریلهای ثابت عملاً امکانپذیر نیست. دریل مگنت با قابلیت اتصال مستقیم به سطوح فلزی و امکان انجام سوراخکاری دقیق در موقعیتهای دشوار، کار نصب قطعات را سریعتر و ایمنتر میکند و بهرهوری پروژه را افزایش میدهد.
از سوی دیگر، در صنایع بزرگ تولیدی مانند کارخانههای فولادسازی یا ماشینسازی مانند کارخانه فولاد مبارکه اصفهان، استفاده از دریل ستونی برای سوراخکاری دقیق قطعات فلزی بسیار رایج است. در محیطهای کارگاهی که تولید انبوه قطعات با دقت بالا اهمیت دارد، دریلهای ستونی با ثبات ساختاری، هدایت دقیق مته و ظرفیت بالای سوراخکاری، بهترین گزینه محسوب میشوند. در ساخت قطعات سنگین برای صنایع نفت، گاز و پتروشیمی، دریل ستونی نقش محوری در تضمین کیفیت سوراخکاری و یکنواختی محصولات ایفا میکند.
این تجربهها نشان میدهد که در عمل، هر یک از این دستگاهها با توجه به ماهیت پروژه و شرایط کاری، میتوانند به بهبود سرعت، کیفیت و بهرهوری عملیات سوراخکاری کمک کنند.
نتیجهگیری نهایی
دریل مگنت و دریل ستونی هر دو از ابزارهای حیاتی در صنایع فلزی و عمرانی به شمار میآیند. هرچند هدف اصلی هر دو دستگاه، سوراخکاری دقیق فلزات است، اما تفاوتهای فنی و کاربردی آنها باعث میشود که انتخاب صحیح میان این دو، نقش مهمی در موفقیت پروژه داشته باشد.
دریل ستونی با ارائه دقت بالا، ثبات ساختاری و ظرفیت مناسب برای تولید انبوه قطعات، بهترین گزینه برای محیطهای کارگاهی و پروژههایی با حجم بالای سوراخکاری ثابت است. در مقابل، دریل مگنت با قابلیت حمل، اتصال سریع به سطوح فلزی و امکان کار در موقعیتهای متنوع، ابزار ایدهآلی برای پروژههای ساخت و نصب در محل، تعمیرات صنعتی و کار در شرایط دشوار محیطی به شمار میآید.
در نهایت، انتخاب بین دریل مگنت و دریل ستونی باید با توجه به نوع پروژه، میزان نیاز به جابهجایی، دقت مورد نیاز و شرایط کاری صورت گیرد. ارزیابی دقیق این عوامل به کاربران کمک میکند تا ابزاری را انتخاب کنند که نه تنها نیازهای فنی پروژه را برآورده کند، بلکه بهرهوری، ایمنی و کیفیت عملیات سوراخکاری را نیز به حداکثر برساند.